High-Volume Heat
Battle Rifle Company Puts Its State-Of-The-Art
AR Through A 10,000-Round Test
What pops to mind when you think of a reliable military firearm? The M1 Garand seems fairly well respected. The Browning 1919 machinegun runs about forever, no matter what. The timeless Avtomat Kalashnikova sets the standard for everything else. All of these guns, however, represent 1930’s-era technology. Surely in the Information Age we can do better.
Iron is the most common material by mass on planet earth and is the fourth most common element in the earth’s crust. Elemental iron is actually softer than aluminum, but by combining it with trace elements like cobalt, carbon, nickel and chromium we can make it do some of the most extraordinary things.
Left to its own devices, iron corrodes badly in the presence of oxygen. However, mix in around 18 percent chromium and you get stainless steel, a remarkably resilient material. I have an acquaintance who regularly cleans his stainless steel handguns by locking the actions open and running them through the dishwasher. While I myself am not quite so bold, he seems to have had good luck with it.
Extending bore life in firearms producing ridiculously high chamber pressures and designed for astronomical round counts is a timeless challenge. While metallurgical solutions of various sorts have been tried with varying degrees of effectiveness, classic chrome plating is hard to beat. Elemental chromium is actually highly unstable and passivates instantly in the presence of oxygen. However, the resulting byproduct, though only a few atoms thick, is remarkably stable and is sufficiently shiny to make you squint when you glance at the bumper of a classic American muscle car in bright sunshine.
Most Combloc guns like the AK-47, RPD, PK, and RPK sport chrome-lined barrels and chambers that contribute substantially to their well-deserved reputation for reliability. Chrome plating the bores and chambers of early M16 rifles went a long way towards addressing this weapon’s well-publicized weaknesses soon after its ill-timed introduction.
Cryogenic Treatments
The term “cryogenically-treated” is tossed about these days in regards to rifle barrels in particular. In this case, steel is carefully prepared so it possesses the right concentration of Austenite at room temperature. Austenite is the term used to describe steel with a particular crystalline structure. This specific steel is then cooled to around minus 310 degrees F using liquid nitrogen. The resulting metallurgical transformation introduces a larger proportion of Martensite, another unique form of steel, into the material’s crystalline structure greatly enhancing both strength and hardness. This process produces superb wear resistance equating to long barrel life in the face of high-round counts.
This process also improves corrosion resistance while removing residual stresses. Cryogenic treatment is an evolving science and it produces properties in appropriate steels only dreamt of a generation ago.
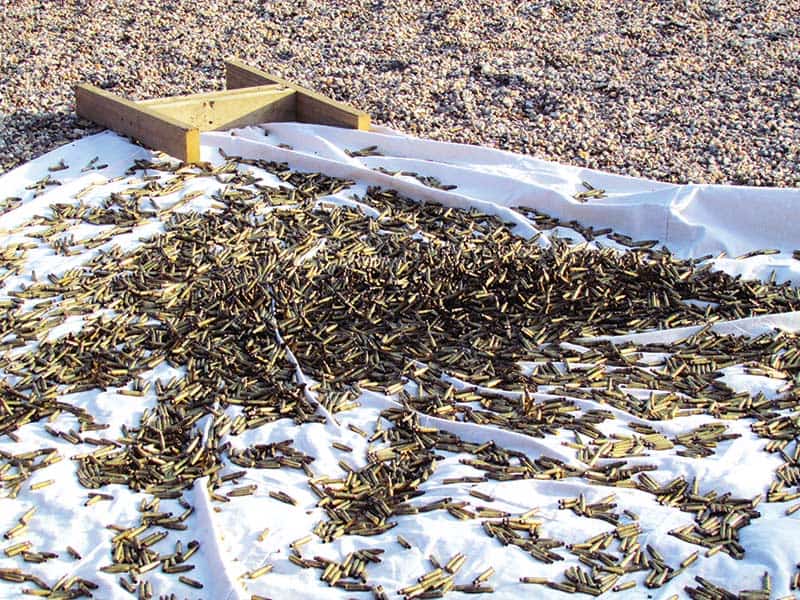
10,000 rounds of empty brass are both voluminous and heavy. It took three of the crew to heft all
of it into the back of a pickup truck at the end of a long day at the range. At the end of the session
Will’s trigger finger cramped and he sported a shoulder bruise comparable to a long day in the dove
field running a 12-gauge.
Coatings
Nickel boron coatings are products of an autocatalytic process. The science behind these innovative metallic coatings is fairly young with much of the development having occurred since the turn of the most recent century. Parts subjected to nickel boron treatments have unprecedented lubricity, minimizing frictional effects. Such treatments are commonly used in ship propellers, guides for paper handling equipment and a variety of car and truck transmission components. Nickel boron treatments also make for superb gun parts. This coating makes firearm components almost impervious to corrosion and imparts an innate “slipperiness” allowing parts so treated to slide across each other like greased glass.
Lots of gun companies make specious claims regarding the reliability of their products. It is easy to toss around terms like “milspec” without really knowing what it means. Additionally, simply because Uncle Sam is satisfied with it doesn’t necessarily mean it is as good as it can possibly be. In the case of a new friend named Chris, the owner of Battle Rifle Company in Houston, Texas, he thought he would start from scratch and establish his own standards.
Battle Rifle Company is a different sort of rifle company. They hand build each of their guns to the customer’s specifications and have carved out a tidy niche producing weapons for both law enforcement and armed citizens that are unquestionably adequate to protect life, limb, home and hearth. BRC has mastered the art of reliability in an AR rifle.
BRC contracts their parts to proprietary specifications. Ongoing quality assessment ensures parts remain up to spec. They lap their upper receivers for a smoother finish. They hand finish the internals of their receivers to remove any high spots or imperfections for a quicker break in. BRC trues up the front of each receiver for better barrel lockup and improved accuracy. They use chrome silicon buffer springs rated for at least 50,000 cycles before appreciable wear. BRC employs 7075-T6 aluminum in both the upper and lower receivers as well as the buffer tube and rails for better wear resistance and longer life. Each rifle is hand built by craftsmen.
Chris is a former infantry officer who is passionate about his weapons. He surrounds himself with combat veteran trigger pullers from all the armed services who know exactly what a combat rifle needs to be. Their end products are refined tactical art.
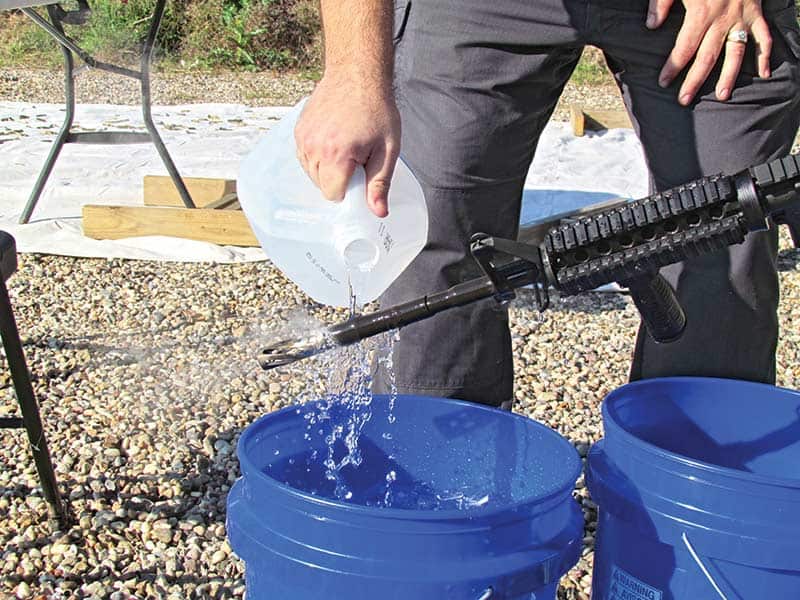
A laser thermometer logged temperatures between 300-round strings of fire typically hovering
around 400 degrees F at the gas block. Every 300 hundred rounds cold water was poured over
the barrel and forearm to cool the gun before immediately cranking up again. The amount of heat
shock on the rifle was incredible yet it never slowed down.
Put Up Or Shut Up
The day started cool and comfortable at a spacious outdoor range near Houston, Texas. Ten cases of Federal M193 5.56mm ammunition were stacked on the range table along with 20 brand new steel 30-round magazines. Two empty 5-gallon pickle buckets were in attendance along with a dozen gallons of water and a cooler filled with Gatorade. The rifle was an otherwise unremarkable off-the-rack Battle Rifle Company BR4 Spartan.
The Spartan is BRC’s basic no-frills tactical rifle. It sports a railed fore-end, a chrome-lined cryogenically-treated barrel, a flip-up rear sight, and an internal fire control group treated with a nickel boron surface treatment. The flash suppressor is a proprietary design cut from unfinished stainless steel. The rifle was a typical example of BRC’s standard offerings—no heavy barrel, no special gimmicks and no magic pixie dust. This particular rifle did have an aluminum vertical handgrip installed. This was a necessity. Before the day was out this gun would get hot.
The regimen was simple. We each took 10 loaded 30-round magazines to the rifle and ran them as fast as we could. After the last magazine was empty we measured the temperature of the gas block with a laser thermometer and then poured cold water over the rifle to cool it back down before starting the next 300-round string. With the exception of a 1-hour break for lunch we rotated shooters and otherwise pushed that long-suffering rifle just as described for 8 full hours. This one gun consumed $4,000 worth of ammunition in a single day. The magazine springs started to get tired after around 7,000 rounds and no longer reliably held the bolt open after the last round. We swapped to a new set of magazines and the bolt locked back without a hiccup until the end of the day. During the course of 10,000 non-stop rounds the rifle had three stovepipe stoppages, each of which was painless to clear. The amount of abuse that rifle withstood was literally breathtaking. In the final magazine of the day, one of our shooters hit a quarter at 40 meters. After the day’s festivities were complete a few bystanders ran another 200 rounds through the gun just for giggles.
We lightly lubed the rifle at 2,500, 5,000 and 7,500 rounds. We replaced the gas rings and wiped down the bolt and carrier at the 5,000 round mark. We caught the empty brass in a tarp and it took three of us to lift it into the truck. At the end of the day the guts of the rifle were utterly caked in funk but it never even slowed down. All in attendance were amazed to find the rifle actually seemed smoother and more accurate at the end of the day than it had at the beginning. No kidding, I had bruises on my right shoulder and my trigger finger was cramping before it was all over.
Many of the Information Age attributes of the Battle Rifle Company BR4 Spartan that allowed it to consume 10,000 rounds in less than 8 hours without a mechanical failure were simply not available back in the age when Browning and Kalashnikov were designing their guns. Just as subsequent technology took space probes to Mars and planted cell phones in our pockets, these same technological advancements in materials science now produce weapons significantly more capable than their forebears.
Not all AR rifles are created equal. Cheap parts make for cheap guns. While the AK has indeed set the standard for reliability for the past 60 years, I can’t see a Kalashnikov running 10,000 rounds in a single day without a noteworthy failure. When artisans like Chris at Battle Rifle Company meld state-of-the-art materials science and engineering with the proven Stoner AR-15 platform the resulting accuracy, performance, and reliability are little short of incredible.
Maker: Battle Rifle Co.
1056 Hercules Ave.
Houston, Texas 77058
(281) 777-0316